Nasschemische Formgebungsverfahren
Unter nasschemischen Formgebungsverfahren werden vorwiegend Technologien verstanden, bei welchen eine Suspension, eine Paste oder ein Schlicker auf der Basis von Pulverpartikeln zu Bauteilen, Strukturen oder Beschichtungen prozessiert werden. Ebenfalls unter diese Rubrik fallen die Techniken, welche ein Sol verarbeiten.
Das IEK-1 verfügt über eine breite Palette an Dick- und Dünnschichtverfahren die sowohl zur Herstellung von ebenen als auch dreidimensional strukutrierten und einerseits dichten wie auch porösen Strukturen dienen.
Neben der Anlagentechnik sind auch die Methoden zur Charakterisierung der flüssigen Vorstufen und auch der Schichten und Bauteile verfügbar. Zu nennen sind hier u.a. Partikelgrößenanalyse, BET-Oberfläche, rheologische Eigenschaften, Topographie, Licht-, konfokale und Rasterelektronenmikroskopie, Röntgendiffraktometrie usw.
Nach der Herstellung der Strukturen bzw. deren Beschichtung stehen auch diverse Trocknungs- und Sintertechnologien zur Verfügung (Öfen bis 2000°C; Luft, Vakuum, Inertgase).
Pulverspritzguss
2-Komponentenspritzgussanlage: Fabrikat Arburg, 370U 2K allrounder 700-100-100; Verarbeitung von zwei Spritzgussmassen in einer Anlage durch Anwendung eines geeigneten Werkzeugs mit zwei Kavitäten.
Folien- und Mikrofoliengießen
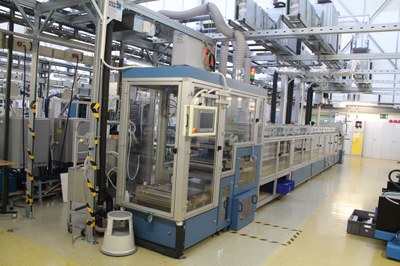
Mittels des Foliengießens können je nach Anlage zweidimensional ausgedehnte kontinuierliche Strukturen unterschiedlicher Gießdicken erzeugt werden. Die Sinterdicken liegen im Bereich von ca. 5 bis 1000 µm. Das Verfahren dient unter anderem zur Herstellung von Substraten für die Hochtemperatur-Brennstoffzelle (SOFC) und Gastrennmembrane.
Anlagen: Technikumsanlage der Firma SAMA; Mikrofoliengießbank: in Beschaffung
Siebdruck
Mittels des Siebdruckens können keramische und metallische Schichten in Dicken von ca. 10 bis 100 µm auf porösen oder dichten Substraten aufgetragen werden.
Derzeit wird es verwendet, um Funktionsschichten der Hochtemperatur-Brennstoffzelle (Anode, Elektrolyt, Kathode) und Zwischenschichten (mesoporöse Schichten) für die Membrantechnologie herzustellen.
Nasspulverspritzen
Mittels des Nasspulverspritzens (engl. wet powder spraying, kurz: WPS) können ebene, runde und auch dreidimensionale strukturierte (nicht hinterschnittene) Bauteile mit Schichten belegt werden. Das WPS -Verfahren kann Schichtdicken zwischen 5 und ca. 150 µm erzeugen (Mehrfachbeschichtung). Derzeit werden beispielsweise die metallischen Interkonnektoren der Hochtemepratur-Brennstoffzelle mit Schutz- und Kontaktschichten über WPS beschichtet.
Schleuder- und Tauchbeschichtung
Beim Schleuderbeschichten (spin coating) werden ebene Strukturen mittels eines Sols oder einer Suspension über Rotation des zu beschichtenden Bauteils beschichtet. Erzielbare Schichtdicken liegen in der Regel unter 2 µm. Beim Tauchbeschichten (dip coating) wird das Bauteil entweder vertikal in eine Suspension/ein Sol oder durch eine Teilkreis-Bewegung in das Beschichtungsmedium getaucht. Auch dieses Verfahren eignet sich hauptsächlich für mikrometerdünne Schichten.
Sinteranlagen (Schutzgas/Vakuum)
Hersteller: Thermal Technology, max. Temperatur 1650°C, max. Abmessungen 300x 300x300 mm³, Schutzgas Ar, H2, Ar/H2, Vakuum, Absaugvorrichtung zum Entbindern, Heizelemente Mo.
Hersteller Fa. Gero, HV-HTK 25 Mo/16-2G, max. Temperatur 1600°C, max. Abmessungen 250x400x250 mm3, Schutzgas Ar, Vakuum, Absaufvorrichtung zum Entbindern, Heizelemente Mo.
Thermisches Spritzen
Beim thermischen Spritzen werden partikelförmige Ausgangsstoffe als Pulver oder Suspension in eine Heißgasfackel injiziert, aufgeschmolzen und auf das Substrat hin beschleunigt. Vielfältige Prozessparameter wie die Gaszusammensetzung, der Gasfluss, der Strom, die Spritzdistanz, die Partikelgrößenverteilung, der Trägergasfluss, der Umgebungsdruck usw. beeinflussen den Aufschmelzgrad und die Geschwindigkeit der Partikel und haben so einen signifikanten Einfluss auf die resultierende Mikrostruktur, Haftung und den Spannungszustand.
Die Heißgas- und die Partikeleigenschaften im Fluge können analysiert werden, um ein verbessertes Verständnis der Prozesse zu erhalten und die Qualität zu sichern.
Plasmaspritzen
Beim Plasmaspritzen werden partikelförmige Ausgangsstoffe in einem Plasmastrahl aufgeschmolzen und auf das Substrat hin beschleunigt, der durch Ionisation eines Gasstroms erzeugt wird.
Das atmosphärische Plasmaspritzen (APS) eignet sich besonders für die Abscheidung von Keramiken, insbesondere Oxidkeramiken für Wärmedämmschichten.
Brenner: Triplex II, TriplexPro-210, Axial III, F4, 9MB, F100 Connex (Innenbeschichtungen)
Das Suspensions-Plasmaspritzen (SPS) ist ein APS-Prozess, bei dem eine flüssige Suspension als Vorstufe eingesetzt wird. Dies ermöglicht die Verarbeitung von Partikeln im Sub-Mikrometerbereich und somit neuartige, mikrostrukturierte Schichten.
Brenner: Triplex II, TriplexPro-210, Axial III
Beim Low Pressure Plasma Spray (LPPS) bzw. Vakuum-Plasmaspritzen (VPS), können keramische und besonders metallische Schichten hergestellt werden, wobei eine Sauerstoffaufnahme vermieden wird.
Brenner: F4, TriplexPro-200, O3CP
Das Niedrigdruck-Dünnfilm-Plasmaspritzen (LPPS-TF) ist eine Weiterentwicklung des Vakuum-Plasmaspritzens bei niedrigem Druck. Dies ermöglicht die Abscheidung dünner, gasdichter Schichten.
Brenner: F4, TriplexPro-200, O3CP
Das Plasma-Spray-Physical Vapor Deposition (PS-PVD) findet ebenfalls bei niedrigem Druck statt, jedoch ist die Leistung noch weiter erhöht. Mit geeigneten Pulvern ist die Abscheidung neuartiger, kolumnarer Strukturen sogar aus der Dampfphase ist möglich.
Brenner: O3CP
Kaltgasspritzen
Beim Kaltgasspritzen expandiert ein moderat vorgewärmtes, komprimiertes Gas durch eine Laval-Düse und erreicht sehr hohe Geschwindigkeiten im Überschallbereich. Wenn beim Auftreffen der Pulverpartikel auf das Substrat eine vom Material abhängige, kritische Geschwindigkeit erreicht wird, werden diese plastifiziert und es entstehen fest haftende, dichte Schichten. Das Verfahren eignet sich besonders für oxidationsempfindliche Materialien.
System: Kinetiks 8000
Hochgeschwindigkeits-Flammspritzen
Im Gegensatz zum Plasmaspritzen ermöglicht das Hochgeschwindigkeits-Flammspritzen deutlich höhere Partikelgeschwindigkeiten bei vergleichsweise moderaten Temperaturen der Brenngasflamme. Daher ist der Prozess besonders geeignet für verschleißfeste Legierungen sowie MCrAlY-Haftvermittlerschichten.
Brenner: DJ2600, DJ2700, Hybrid-Aircap
Wasserstoff-/Methan-Sauerstoffprozess mit Air/N2-Mantelgas
Anlagentechnologien
Aktuell verfügt das IEK-1 über drei verschiedene PVD-Anlagen und eine CVD-Anlage mit jeweils unterschiedlichen Anwendungsbereichen.
PVD Anlage CS 400 ES
Die PVD-Anlage CS 400 ES (Von Ardenne GmbH) wird für luftunempfindliche Beschichtungen im Bereich Elektrochemische Speicher und Brennstoffzellen genutzt und ermöglicht Kathodenzerstäubung ("Sputtern") im Gleichstrom (DC)- und im Hochfrequenz (RF-)-Betrieb, sowie Elektronenstrahlverdampfung. Beide Prozesse können auch reaktiv, d.h. in Anwesenheit eines Gases, mit dem das Material in der Gasphase reagieren kann, durchgeführt werden. Zur Einstellung der Morphologie können die Beschichtungen bei Temperaturen bis 800 °C und wahlweise mit zusätzlicher Ionenunterstützung erfolgen. Dabei können Substrate bis zu einem Durchmesser von 7 Zoll (ca. 17,5 cm) beschichtet werden.
PVD Anlage CS 800 ES
Die PVD-Anlage CS 800 ES (Von Ardenne GmbH) komplettiert die Anlagentechnologie der CS 400 ES, sie verfügt insbesondere über auf die Herstellung von Dünnschichtbatterien abgestimmte Erweiterungen. Der modulare Aufbau aus zwei Sputter- und einer Elektronenstrahlverdampferkammer ermöglicht die Abscheidung von kompletten Batterien innerhalb des Systems ohne Ausbau der Proben aus der Anlage. Dadurch werden Kontaminationen auf ein Minimum reduziert und die Qualität der erhaltenen Zellen deutlich erhöht. Darüber hinaus ist die Anlage an ein Glovebox-System angebunden, so dass auch luftempfindliche Schichten hergestellt und direkt nach der Synthese erste Analysen ohne Unterbrechung der inerten Atmosphäre durchgeführt werden können.
PVD Anlage CC800/9
Die PVD-Anlage CC800/9 (Cemecon AG) beschichtet mittels Hochenergieimpulsmagnetronsputtern. Dies ermöglicht unter anderem eine verbesserte Haftung der Schichten und eine homogene, dichte Schicht auch auf komplexen Geometrien.
CVD Anlage
Die Anlage zur chemischen Gasphasenabscheidung erlaubt den Einsatz metall-organischer Vorstufen (sog. Prekursoren; diese Verfahren heißt dann auch MO-CVD (engl. metal organic chemical vapor deposition)) sowie eine Prozessführung, bei der die Schichten in einzelnen aufeinander folgenden Atomlagen aufgebaut wird (engl. atomic layer deposition, kurz: ALD). Durch den Einsatz metallorganischer Prekursoren können vergleichsweise niedrige Beschichtungstemperaturen im Bereich von ca. 100-300°C erreicht werden. Der ALD-Modus erlaubt auch die Beschichtung der inneren Oberflächen von porösen Materialien. So können z.B. Diffusionsbarieren, Oxidationsschutzschichten oder biokompatible Schichten aufgebracht werden.
PVD/CVD
Mikrostrukturiert, leistungsfähiger, preisgünstiger: Die Mikroelektronikindustrie hat vorgemacht, wie auch hochkomplexe Systeme mit massenfertigungstauglichen Herstellungsverfahren besser und bezahlbarer werden können. Auch für Batterien ist die effiziente und damit wirtschaftliche Herstellung ein ganz wichtiger Aspekt. Am IEK-1 wird dabei auf sogenannte Gasphasenabscheidungsprozesse gesetzt. Hier unterscheidet man grundsätzlich zwei Arten: physikalische Gasphasenabscheidung (engl.: physical vapor deposition, kurz: PVD) und chemische Gasphasenabscheidung (engl.: chemical vapor deposition, kurz: CVD).
Bei der physikalischen Gasphasenabscheidung (PVD) wird ein Material z.B. durch Verdampfen oder Zerstäuben auf atomarer Skala in die Gasphase überführt. Das Gas trifft auf die zu beschichtenden Proben und scheidet sich dort, je nach Versuchsdauer, als nanometer- bis mikrometerdünne Schicht ab. Während des gesamten Beschichtungsprozesses - Überführen in die Gasphase, Bewegung zu den Proben und Kondensation auf der Probenoberfläche - ändert sich nur der Aggregatszustand des Werkstoffs: von "fest" oder "flüssig" zu "gasförmig" und wieder zu "fest". Es bleibt aber grundsätzlich chemisch dasselbe Material.
Anders bei der chemischen Gasphasenabscheidung (CVD): Hier werden Gase zu den Proben geleitet, die auf dem Weg zur Probe bzw. an der Probenoberfläche chemisch reagieren. Ein Teil der chemisch reagierten Substanzen bleibt an der Oberfläche und bildet die Schicht.
Prinzip
Bei der physikalischen Gasphasenabscheidung wird ein Material auf atomarer Ebene verdampft. Das Gas trifft auf die Probe und wird als dünner Film abgeschieden, je nach Abscheidungsdauer im Nanometer- oder Mikrometermaßstab. Während des gesamten Abscheidungsprozesses - Verdampfung - Übertragung auf die Probe - Kondensation auf der Probenoberfläche - wird nur der Aggregatzustand des Materials geändert: von "fest" oder "flüssig" zu "gasförmig" und zurück zu "fest". Normalerweise wird das Material während des Abscheidungsprozesses nicht verändert.Bei der chemischen Abscheidung aus der Gasphase wird ein Gas auf die Probe übertragen, und es findet eine chemische Reaktion während des Transports oder auf der Probenoberfläche statt. Teile des reagierten Materials verbleiben an der Oberfläche und bauen die Schicht auf.
Rasterelektronenmikroskopie/ energiedispersive Röntgenanalyse (REM/EDX)
Leistungen und Kompetenzen
- Qual./quant. Mikrobereichsanalyse (Punkt, Linie, Fläche) mit energiedispersivem Si(Li)-Detektor (EDX), sowie Kathodolumineszenz
- Ergebnisdokumentation in digitaler Form und Bereitstellung im Intranet
- Hochaufgelöste Oberflächen- und Gefügeabbildung im Topografie-/Materialkontrast (E = 0.3 ... 30 keV, Vergr. 20 ... 500 000fach)
Geräte
Anlagen für die Probenpräparation
- Sputterbeschichtungsanlage SCD050 (Au, Pt)
- Leica Sputtercoater EM ACE200 für Pt und Kohlenstoff
- Hitachi IM4000 zur Politur von Bruchfläche und Querschliffen mit Ar-Ionen
Rasterelektronenmikroskope
- Zeiss "Ultra55" (FEG-REM) mit EDX (X-Max 80mm2) (Oxford Instruments, INCAEnergy400)
- "Phenom" table top REM (einfaches Tischgerät mit CeB6-Kathode ohne EDX für Abbildung 200-20000x bei 5kV)
Röntgendiffraktometrie (XRD)
Leistungen und Kompetenzen
- Qualitative/quantitative Phasenanalyse an polykristallinen Werkstoffen ( Entflechtung von überlagerten Interferenzdiagrammen komplexer Phasengemische, kristalline Phasen, röntgenamorphe Anteile)
Phasenidentifizierung durch Search-Match mit der ICDD-Datenbank (PDF-2 Release 2010) - Bestimmung und Verfeinerung von Gitterparametern
- Verfeinerung von Kristallstrukturen mittels Rietveld-Analyse
- Ermittlung von Kristallitgrößen und Mikroeigenspannungen
- in-situ Röntgenbeugung bei hohen Temperaturen (T = RT-1873 K) in unterschiedlichen Atmosphären (oxidierend, reduzierend, inert, Vakuum bis 10-4 mbar)
- Bestimmung von (lokalen) Resteigenspannungen in Oberflächen und Schichten (sin2(Psi)-Verfahren in Omega- und Psi-Geometrie), Spannungsmapping mit ca. 1 mm2 Ortsauflösung
- Orientierungsbestimmung, Texturanalyse
- Untersuchungen an dünnen Schichten und Beschichtungen
- Ergebnisdokumentation in digitaler Form und Bereitstellung im Intranet
Geräte
- Theta-2Theta Diffraktometer mit 66fach Probenwechsler (Bruker-AXS/D4 Endeavor) Proben-Drehtisch, automatische Divergenz-/Streublende, diverse Spaltblenden, Sollerblenden 2.5°, automatischer Empfangsspaltwechsler, Liniendetektor LynxEye, keramische 2 kW Cu-Langfeinfokusröhre
- Universelles Theta-Theta Diffraktometer für Materialuntersuchungen (PANaytical/Empyrean) 5-Achsen-Eulerwiege, Röntgenspiegel, Polykapillar-Halblinse, automatische Divergenzblende, Sollerspalte 0.04 rad, Parallelplatten-Kollimatoren 0.27°/0.18°, Graphit-Sekundärmonochromator, Cu-/Cr-Keramikröhren 2kW
- Hochtemperatur-Ofenkammer (Anton Paar) HTK 1200N bis 1200°C, HTK 16N bis 1600°C
Spezielle Software
- Powder Diffraction File (PDF-2, Release 2010)
- Crystallography Open Database (COD, 10/2014)
- Inorganic Crystal Structure Database (ICSD, online)
- X'Pert Suite (Data Collector 4.3, HighScorePlus 4.1)
- StressPlus, Texture DiffracPlus Evaluation Package V14 (Eva,, Search/Match, DQuant, ...)
- Diffrac-AT 3.3B (Eva, Profile, Search/Match) Total Pattern Analysis Solution Software (Topas 4.2)