Optimisation, airborne applications of low-cost sensors
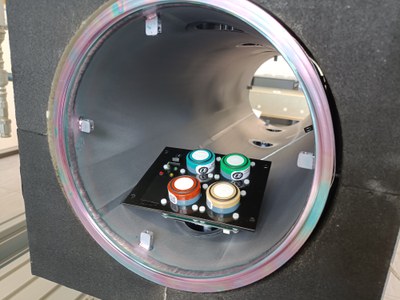
The objective is to optimise low-cost sensors together with the Institute of Energy and Climate Research - Troposphere (IEK-8) in order to use them on mobile and airborne platforms to record pollutant concentrations in the atmosphere - in particular to measure traffic emissions. Here, electrochemical sensors are used to analyse air pollution and air quality up to an altitude of 2 km in addition to the traditional measuring devices used to date. The advantages of these electrochemical sensors over traditional measuring devices are their low weight, low cost and small dimensions. Thanks to these characteristics, these sensors can be used very well on small aircraft.
Climatized Atmospheric Calibration flow Tube System
In the so-called CACTUS project, these sensors are being enhanced with the newly developed system. Here, the temperature, humidity and pressure in a SilcoNert-coated stainless steel tube are monitored and changed within seconds in order to recognise and correct possible sensor faults. To use these sensors, it is essential to characterise them in a defined atmosphere and calibrate them regularly. The Cactus system, a calibration platform for electrochemical sensors, was developed for this purpose.
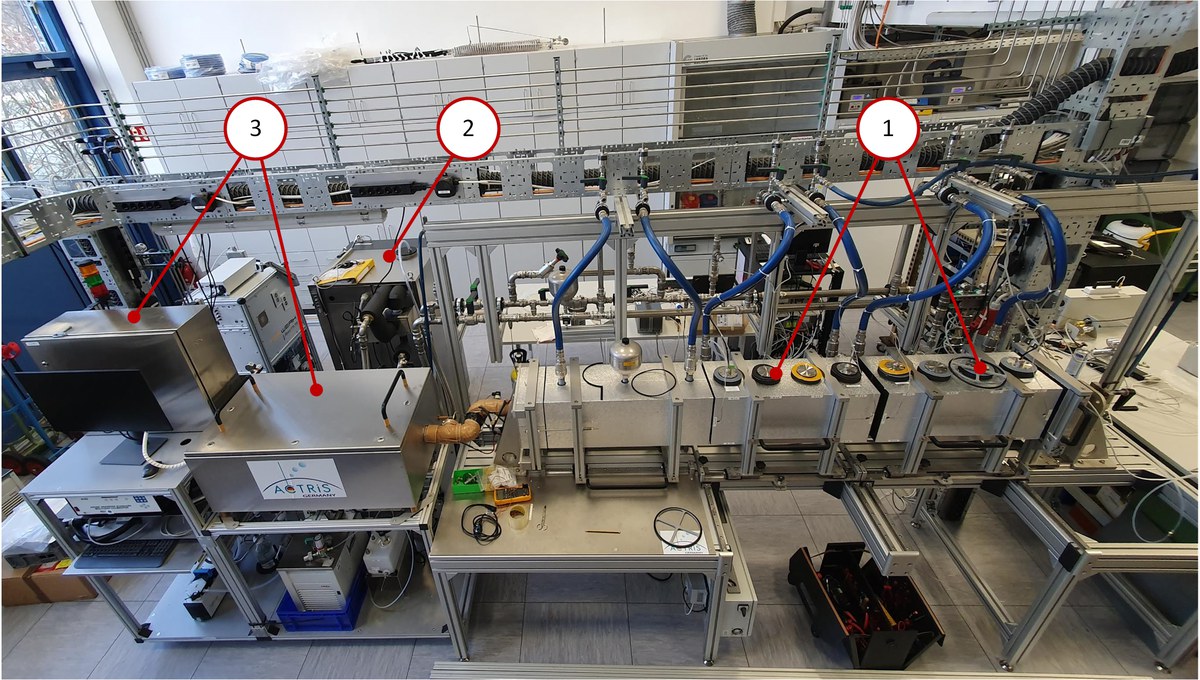
Technical Challenges
The challenge in the concept development, planning and realisation was, on the one hand, the diversity and scope of the process technology. A large number of gases and particles have to be dosed, mixed, tempered, humidified and pressure-controlled while at the same time taking into account the respective risks, e.g. from the gases themselves or the pressurisation of all components. In addition, the atmosphere chamber is a highly complex component, which was manufactured in a double-walled design from special, highly corrosion-resistant steel and provided with a vapour-deposited inert coating at over 400 °C in accordance with the framework conditions of the Pressure Equipment Directive.
In the centrepiece of the system, the atmosphere chamber, the sensors are exposed to the desired conditions and calibrated. The ambient conditions can be varied as follows:
Temperature range for the generated gas mixture and all components in contact with the gas: -20°C to +45°C
Temperature change rate: 2 °C/min
Generation of a gas mixture from the following components: Synthetic air, CO2, CO, NO, NO2, O3, Volatile Organic Compounds (VOC's) and aerosols
Humidity: 0 to 95 % r.h. without formation of condensation through tempered surfaces
Air pressure: 750 to 1,020 mbar absolute pressure
All components of the atmosphere chamber that come into contact with gas are precisely temperature-controlled. A double-walled design and temperature control using liquid refrigerant were provided for this purpose. In addition, all components in contact with the gas were provided with an inert coating (Silconert 2000). Racks are used for gas generation and conditioning of the test gas. The various gases, particles and VOCs are added here, the gas is pre-tempered, humidified and then passed to the mixing chamber. From there, the process gas enters a further heat exchanger for post-tempering and is then channelled into the atmosphere chamber. A powerful refrigeration unit with a temperature control capacity of 10 KW and a volume flow of liquid refrigerant of 180 litres/min. is used to implement rapid temperature changes in the test gas and all components in contact with the gas (e.g. the atmosphere chamber itself, heat exchanger, etc.).
More Information: project page IEK-8