JULIAC - TRACKING CLIMATE CHANGE
"Clean air" is a highly topical issue and puts the self-cleaning of the atmosphere at the centre of many studies. At Forschungszentrum Jülich, an important part of atmospheric research is carried out in the SAPHIR atmospheric chamber. In a 20 metre long Teflon tube, our colleagues from the Institute of Energy and Climate Research (IEK-8, Troposphere) investigate the composition of the air, for example how much ozone or particulate matter it contains.
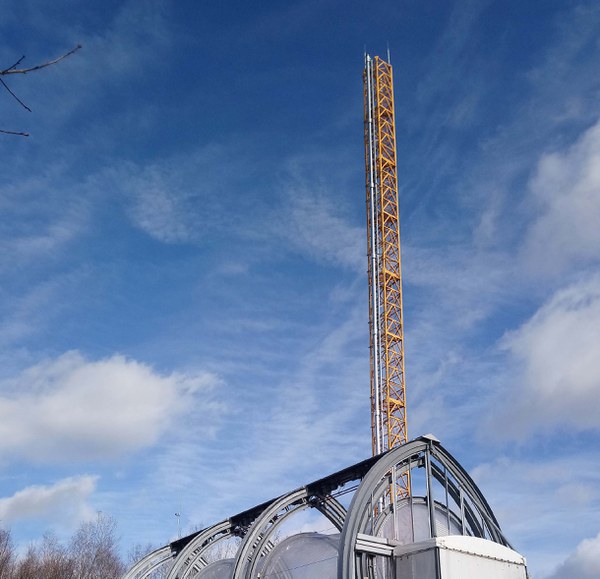
OUTSIDE AIR SUPPLY FOR THE SAPPHIRE CHAMBER
To do this, the seasonal change in the day and night chemistry of the radicals that are important for the self-purification of the atmosphere, i.e. the changing emission patterns of trace gases over the course of the year, is analysed.
To do this, SAPHIR must be supplied with air, which is drawn in from a height of around 50 metres (above ground level). Here it is important that the surrounding trees and buildings are clearly towered over. This ensures that the air drawn in is decoupled from the direct influence of local emissions, e.g. from passing cars.
These investigations have been carried out on the grounds of Forschungszentrum Jülich since the end of 2018. The air composition on the campus is characterised by local emissions of biogenic, volatile organic compounds from the surrounding mixed forest, as well as by anthropogenic trace gases from traffic, cities and agriculture in the surrounding area. The air to be investigated is channelled through SAPHIR, where the chemical composition and chemical processes taking place under the influence of sunlight are analysed using a variety of measuring instruments. The measured data sets are used to check and improve atmospheric chemistry models, which are required for the regional and global prediction of atmospheric air pollutants.
JULIAC, as quickly as possible and with little contact
The aim of the Juelich Atmospheric Chemistry Study (JULIAC) project is to minimise changes in the composition of the air with regard to its content of trace gases (ozone, nitrogen oxides, sulphur dioxide, hydrocarbons) and fine particles (< 2.5 µm). This means that all components of the gas conveying system must be designed in such a way that the loss of trace gases and particles on the walls of the components is minimised and that the surfaces that are in contact with the air do not themselves act as a source of contamination. For example, hydrocarbons from oil and lubricants used in a positive displacement blower.
Technical challenge
All parts were designed to minimise contamination of the air. Particular attention was paid to suitable materials for complex components. Most of the surfaces are coated with a special patented coating to prevent trace gases and radicals from reacting with the surfaces of the components. As the trace gases and free radicals in the air are very reactive, the duration of the reaction must also be minimised during transport. These requirements can best be met by trying to minimise the surface area with which the air comes into contact from the outset. This means that the pipework is positioned as close as possible to the SAPHIR chamber and that the air is drawn in and transported into the chamber at a high speed. In addition to the pipework, the main component of the instrument is a turbo compressor, which enables the necessary high air flow rate.
Another technical challenge is the pressure loss within the pipework, which causes a significant drop in temperature which can lead to condensation. A heat system was therefore developed. This prevents condensation from forming in the temperature-controlled pipework.
The regulation of the volume flow to the SAPHIR chamber is also key. Only a small proportion of the air drawn in is led into the SAPHIR chamber, the majority is released back into the environment. Thanks to the control system developed in the ZEA-1, the required pressure difference of the SAPHIR chamber (approx. 40Pa overpressure to the external pressure) can be realised in addition to the volume flow. At the same time, experimental gases can be added via a small feed. JULIAC allows scientists to carry out a wide range of experiments.
Our collaborations with the colleagues on campus working on SAPHIR are a good example of our understanding of partnership-based collaboration. Whether air pollutants and greenhouse gases or water cycles and plant growth - we use our consulting and development expertise to design, develop and manufacture scientific and technical devices and systems for environmental research, among other things. In close cooperation with scientists, we create unique measuring devices that are not available on the market.
Technical data
Crane tower weight ballast: 120 tonnes
Height of air inlet: 52.5 m
Length of pipework to SAPHIR: 67.8 m
Inner diameter of pipework: ø104 mm
Diameter of the riser pipe approx. ø210 mm
Working range of turbo compressor: 30 - 1000 m³/hour
Volume flow into the SAPHIR chamber: 30 - 250 m³/hour
Cyclone filter performance: all particles over 10 µm (90 per cent) filtered out
Surface temperature of pipework: +2 K to the air temperature
Heating capacity: 6300 W
Automation system: Siemens S7