Battery Storage Systems
Two large battery storage systems have been installed on the campus. The research focuses on the integration and mode of operation of these battery systems in an energy mix with photovoltaics (PV), wind power and hydrogen. The goal is to integrate battery systems into future energy systems in a more efficient, less expensive and space-saving way.
The two battery storage systems differ in terms of storage capacity and power: the high-energy battery system has a capacity of 2,600 kWh and a maximum power of 595 kW, while a high-performance battery system holds a capacity of 525 kWh and has a maximum power of 1500 kW.
The high-energy system is a so-called megapack from Tesla. The high-energy battery system functions as a buffer, storing energy when grid demand is low and feeding energy back into the grid when demand is high.

The high-power system from the manufacturer Riello is used for so-called peak shaving, i.e. for reducing high peak powers in the grid in relatively short periods of time. In addition, it serves as an uninterruptible power supply for a nearby building.
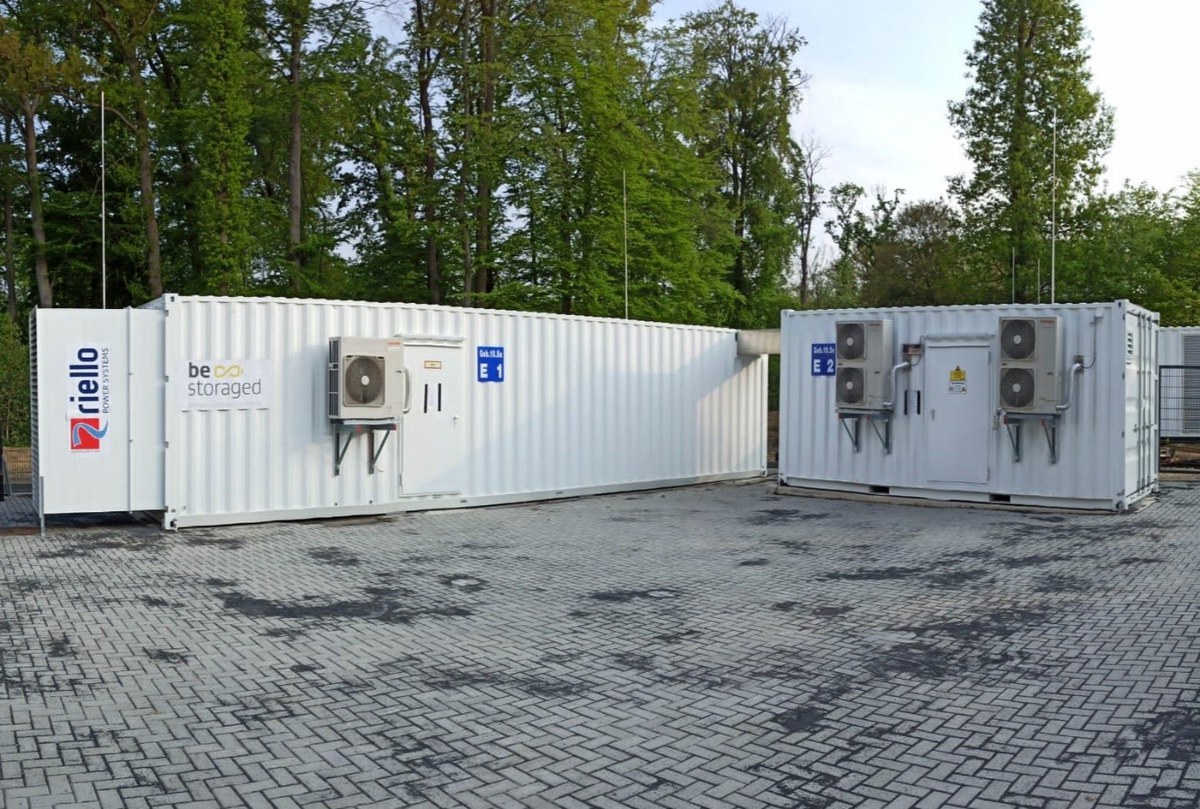
In this context, two main research questions are examined: The first question can be seen from a control perspective and the second question from a "digitalization" perspective. From the control perspective, the research question is how both battery systems can be optimally integrated into a decentralized energy system, where the battery systems are considered as black boxes that can supply or absorb energy. Digitization involves using complex models or a "digital twin" to specifically simulate and study system states in advance. These models also enable simulation calculations to be carried out in parallel with the operation of the plant. The effect of incorporating electrical and electrochemical models into utility-scale energy storage systems is being determined. A new feature here is that these models are used to perform simulations on large stationary battery systems.
Battery cell models (digital twins) are currently being created for stationary battery storage systems. In the end, the behavior of the model should correspond exactly to that of the real battery cell. The battery cell models are extended to pack models, which allow the behavior of all battery cells in the system to be evaluated. This provides information on all operating states such as voltages and temperatures of the entire battery pack. In principle, this means that complex measurements requiring many hardware components are no longer absolutely necessary. As a result, system costs can be reduced. At the same time, power electronics models are also created, which are coupled with the battery models at a later stage of the project. These models make it possible to simulate losses in the power electronics and complete the model for the overall system.
Through model development of these battery systems, operating conditions can be simulated and energy-optimal, cost-effective, and safe operation of the entire LLEC energy system can be targeted. In the process, valuable insights into performance and lifetime under real operating conditions are captured, which are relevant for the innovation of stationary energy storage systems.