Component development
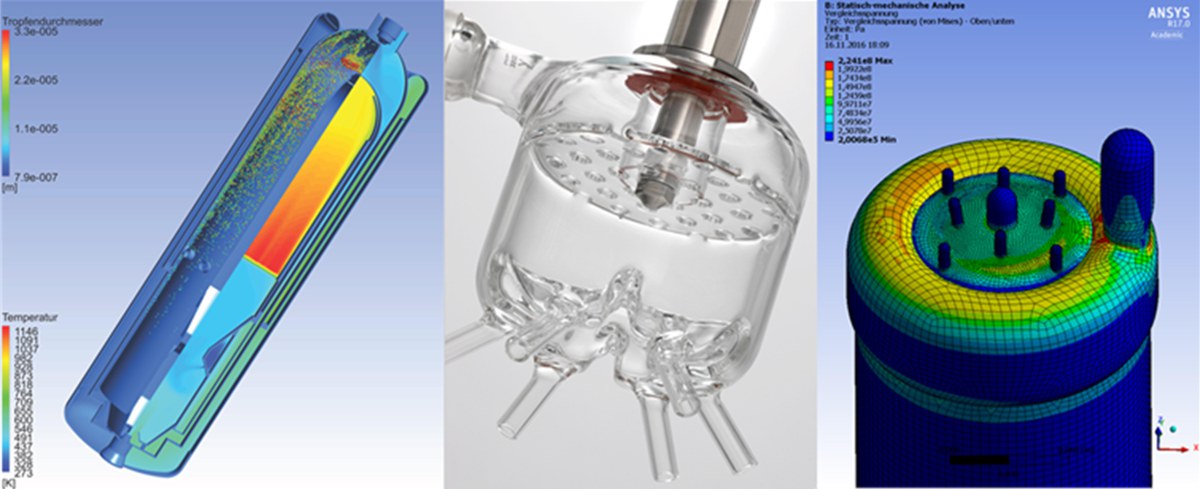
At IET-4, several reformer generations for middle distillates have been developed in the past years. The reformers are able to produce a quantity of hydrogen from conventional diesel fuels that is sufficient for fuel cell outputs between 3 and 50 kWe. The preferred method here is so-called autothermal reforming.
In order to better understand and predict the flow and temperature conditions in the reformer's mixing chamber, computational fluid dynamics (CFD) are carried out in Jülich. This methodology has been continuously developed over the years. Today, not only the reformer's mixing chamber, but the complete reformer with all interactions between reaction, heat recovery, and mixture formation is simulated statically and dynamically using CFD modeling on high-performance computers (HPC). New reactor concepts are verified in glass models with substitute liquids as part of the similarity theory. The design is carried out with commercial CAD programs based on the AD 2000 for pressure vessels. Further steps in component development are the TÜV preliminary inspection, the procurement of materials under consideration of the necessary material certificates, the manufacturing in the central workshop of the Research Center Jülich (ZEA-1), the creation of documents for the declaration of conformity and, last but not least, the TÜV inspection of the pressure vessels.
The CFD-based approach to reactor design was also applied to catalytic combustion and the water-gas shift reaction. This also resulted in several reactor generations for the catalytic burner (3-10 kWe power class) and for the water-gas shift reactor (3-50 kWe power class). The reactor development methodology for fuel gas production is currently being transferred to the reactors for fuel synthesis.
To meet the requirements of mobile on-board power supply systems, the current focus of reactor technology is on the development of compact and lightweight systems. Multifunctional reactor concepts are being developed to integrate system tasks such as start-up and heat exchange into the reactors. The current reformer and the water-gas shift reactor contain electric heating conductors so that the system can be started up autonomously. All reactors have integrated heat exchangers to recover the process heat for educt conditioning.
In the context of the multifunctional reactor design, it is important to develop compact and lightweight reactors. In addition to optimizing the reactors with the help of CFD simulations, the reactor weight must also be optimized. The necessary strength calculations are carried out based on the finite element method (FEM) with ANSYS® Mechanical. The equivalent stresses can be calculated linearly-elastically-ideally plastically with a volume or shell model, whereby the shell models offer a better and more accurate method for calculating thin-walled components.
Another focus of the reactor technology is on the further development of research prototypes for industrial production. As part of a publicly funded project (ADELHEID), the reactors for reforming were transferred to industrial production. In collaboration with the company Presswerk Struthütten, the reformer was optimized in terms of costs and production using a forming manufacturing process. Furthermore, formed parts from industry that enable cost-effective mass production are also being implemented in other chemical reactors. The use of the additive manufacturing process for highly integrated multifunctional reactors is being investigated in collaboration with ZEA-1.