Fuel Processing
Technical catalysts are required for the reforming of liquid and gaseous fuels in the processes used at IET-4. Catalysts are generally highly sensitive to liquid droplets and various trace elements (e.g. sulphur). If a catalyst is wetted with liquid and then rapidly heated by an oxidation reaction, the liquid trapped in the pores can evaporate locally. The resulting pressure surges can destroy the pore structure and thus the entire catalytic converter. Two research topics can be derived from this: the desulphurization of fuels containing sulphur and homogeneous mixture formation.
Desulphurization
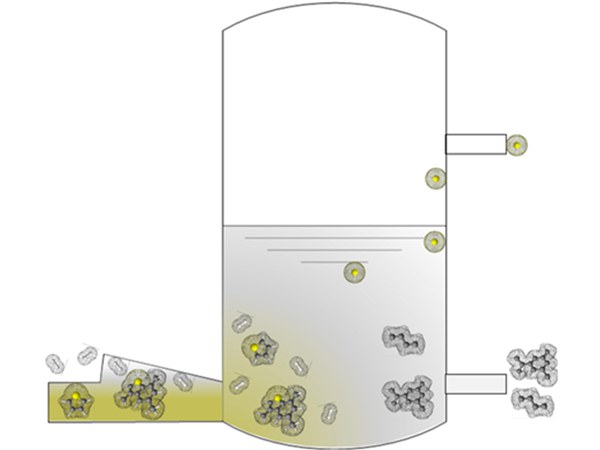
The IET-4 has been working on the desulphurization of liquid fuels since 2005. The focus is on the desulphurization of kerosene and EL heating oil with maximum contents of sulphurous hydrocarbons of 3000 ppm and 2000 ppm. Following a theoretical analysis and selection of processes that are fundamentally suitable for decentralized desulphurization in fuel cell systems, the individual processes were initially investigated on a laboratory scale. Based on the experimental results, two processes proved to be particularly successful: hydrogenation desulphurization with pre-saturation with hydrogen in the liquid phase and a multi-stage process consisting of pervaporation - a special process modification of a gas separation membrane - and adsorption. Hydrogenative desulphurization with pre-saturated hydrogen in the liquid phase is the only process that has the potential for technical implementation in the short term. In the medium to long term, however, combinations of membranes and adsorbents can also play an important role in desulphurization. However, further research is required for this.
The figure above shows in a schematic diagram how the individual molecules react with hydrogen. One hydrogen molecule reacts with the sulphur atom in the thiophene ring to form hydrogen sulphide, a second hydrogen molecule saturates the previous bonds of the sulphur with the two carbon atoms in the thiophene ring. This is shown in the diagram for 2,5,7-trimethyl-benzothiophene and for a simple thiophene. On the product side, butadiene and a polyalkylated benzene molecule are formed. The chemical reaction equations are as follows:
C4H4S + 2 H2 -> C4H6 + H2S
C11H12S + 2 H2 -> C11H14 + H2S
These reactions take place in the gas phase or in the liquid with pre-saturated hydrogen. In the liquid phase, absolute pressures of 40 - 75 bar and temperatures of 330 - 390 °C are required. For the desulphurization of kerosene with approx. 550 ppmw S, which is commercially available in Europe, hydrogen partial pressures of 25.5 bar are required.
Spray formation and fuel evaporation
The atomization of fluids in technical applications is realized by a variety of different injection systems. These differ not only in the type and design of the nozzles, but also in the underlying atomization mechanisms. Three main decay mechanisms can be identified for technically relevant injection nozzles: decay in the jet, in the vane flow and droplet decay in the gas flow.
However, characterizing injection systems solely on the basis of these underlying atomization mechanisms is insufficient. The nozzle type and the specific design of the atomizer are also decisive for technical practice. Technical atomizing nozzles can be divided into four basic types:
- Single-fluid nozzles atomize the fluid using the energy introduced into the fluid via the pressure. They are relatively inexpensive and can be designed as jet-forming or lamella-forming nozzles. Single-substance nozzles based on turbulent jet breakdown are referred to as turbulence nozzles.
- Dual-substance nozzles atomize the fluid in a second gaseous medium. The energy for atomization is usually supplied via the gas flow. If air is used as the atomizing gas, the nozzles are referred to as pneumatic nozzles.
- Mechanical atomizers are single-fluid nozzles in which a thin fluid film formed on a surface of the nozzle is atomized. The energy required for this is provided by a rotational or vibrational movement.
- The special atomizers include impact nozzles and electrostatic atomization systems.
- CFD simulations are an important tool for nozzle and system design. Modeling allows the investigation of complex geometries and the consideration of various material properties. The figure below shows the flow profile and the droplet paths of the fuel injection in the immediate vicinity of the nozzle. The spray cone is at a sufficient distance from the vapor baffle, which is only visible in the flow profile in this illustration. In the further course, the spray cone lies exactly in the flanks of the expanding rotating "vapor lance". This means that the droplets flow in the middle of the superheated steam, ensuring effective evaporation.
