Reforming
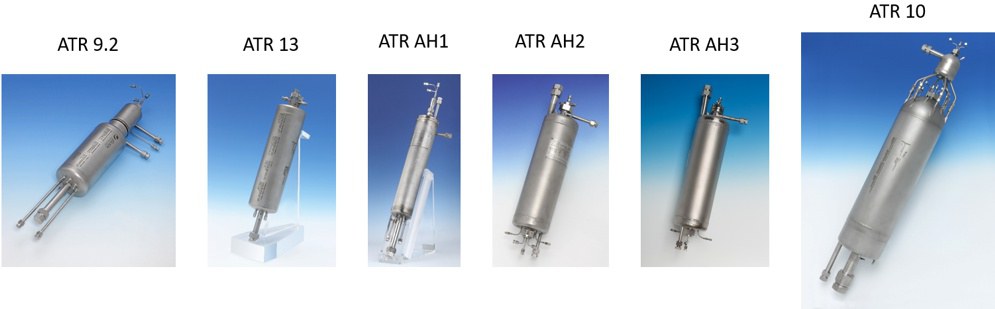
A reactor for autothermal reforming converts the liquid fuel (e.g. diesel) in a catalytic process together with water vapor and air into a hydrogen-rich gas mixture, the so-called reformate. In addition to the target product hydrogen, the reformate also contains significant quantities of carbon monoxide, carbon dioxide, methane, argon and nitrogen. The reactions that take place are summarized in the diagram below:
CₙHₘ + n H₂O | ⟷ | n CO + (m/2 + n) H₂ | endotherm |
CₙHₘ + n/2 O₂ | ⟷ | n CO + m/2 H₂ | exotherm |
CO + H₂O | ⟷ | CO₂ + H₂ | exotherm |
CO + 3 H₂ | ⟷ | CH₄ + H₂O | exotherm |
Several generations of reactors for autothermal reforming have been designed, manufactured and experimentally tested at IET-4 in recent years. They have a wide range of thermal output between 13 kW and 140 kW. What they have in common is that they are equipped with an integrated heat exchanger to provide superheated steam as one of the starting materials for autothermal reforming. Other common features are
- Use of a commercial RhPt/Al2O3-CeO2 catalyst
- Use of a swirl pressure nozzle for fuel injection
- Addition of air to the reaction mixture downstream of the fuel vaporization zone
During a screening of different reforming catalysts in IET-4 it was found that particle growth, fouling and solid state reactions can be used as main reasons for observed deactivation phenomena of the investigated catalysts (Rh/g-Al2O3, Rh/La-Al2O3, Rh/CeO2, Rh/Gd-CeO2, Rh/ZrO2 and Rh/Y-ZrO2). The latest reformer generations were manufactured industrially by a medium-sized German company. This enabled production costs and the use of materials to be optimized. This transfer of production technology from a research institute to a medium-sized company represents an important step towards the commercialization of IET-4's reformer technology.