Structure Formation Processes
Each of the process steps influences the structure of the electrode which affects the efficiency. From the substrate used for the coating over the coating method, drying, the hot pressing parameters – each step is analyzed and chosen carefully with respect to scalability, process efficiency and MEA performance.
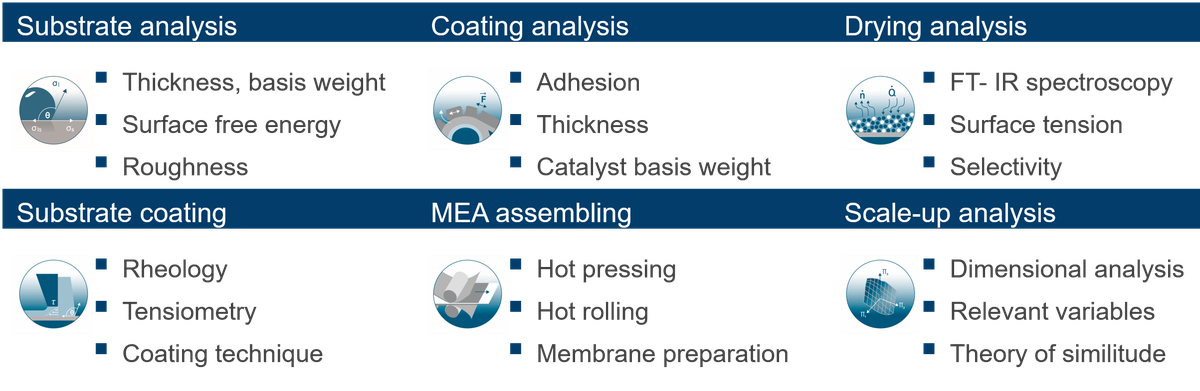
Substrate analysis is one important precursor to achieve homogenous coating results. The focus is on surface morphology, surface free energy, thickness, and basis weight distribution.
The surface free energy is essential for understanding the substrate wettability. The measurement is taken by contact angle measurement with drop shape analyzers and calculated by methods generally used like Owens-Wendt. By the knowledge of the surface free energy and application of the wetting envelope it can easily be seen whether catalyst dispersion wets a substrate or not.

Substrate coating is developed under laboratory conditions with regard to subsequent scale-up to pilot plant dimensions. The coating is applied in laboratory and pilot plant scale by slot die coating technique from 50 mm coating width to 300 mm maximum width.
Rheology of the dispersion
Depending on the rheological structure in the dispersion and the free surface energy of the substrate, the coating process leads to different changes in the dispersion. Using rheological and tensiometric investigations, these influences on the dispersion can be clarified.

Drying the dispersion
During the drying process, the solvents vaporize at different drying rates, which causes the solids in the dispersion to agglomerate to porous structures. This layer formation process is closely interconnected to the time-dependent progression of the chemical composition of the wet layer all the way to the dry electrode. By adapting thermodynamic parameters, this progression can be controlled so that crack formation can be influenced, for example. To analyze these processes, a spectroscopy-based measurement technique was developed at IET-4, which simultaneously enables the reproducibility of the electrode fabrication to be examined

Mechanical analysis
In the roll-to-roll coating process the final layer is coiled up. Afterwards, the layer is transferred to the membrane by hot pressing. To meet these circumstances, adhesion between coating and transfer foil needs to be strong enough that handling the coated substrate like winding and unwinding is possible, but adhesion needs to be weak enough for an entire transfer.
Adhesion properties are analyzed by measuring the tensile strength between the coated layer and the transfer foil. The adhesion characterizing parameters can be analyzed as a function of process parameters like coating thickness or drying temperature.