The object Ian Marius Peters is holding looks like an exquisite bathroom tile: the surface has a dark blue metallic shimmer. Regular silver stripes run across it. “This is a typical silicon solar cell,” explains the physicist. “60 of these tiles make up one standard photovoltaic module.”
More than 2.2 million solar systems are installed in Germany – on the roofs of houses and warehouses, as small balcony power plants or in huge solar parks. With a total maximum output of 60 gigawatts, they supply around 10 per cent of the electricity produced in Germany. In the meantime, however, the first modules have reached the end of their economic life. Technically, they could still supply electricity, but modern solar cells offer a much higher electricity yield than the old systems due to improved efficiency. These are now being successively replaced. The boom years of photovoltaics, between 2009 and 2014, will see the number of aged plants skyrocket. “In the next five to ten years, we will be faced with a flood of decommissioned modules. We should already be thinking about how we want to deal with this,” says Peters. He is researching how the discarded modules can be recycled at the Helmholtz Institute Erlangen-Nürnberg for Renewable Energy (HI ERN), a branch office of Forschungszentrum Jülich.
RECYCLING BY LAW
“The recycling of PV systems is regulated by law in the European Union,” explains the solar expert. “80 per cent of a panel – in terms of weight – must be recycled.” The glass cover and the aluminium frame account for the largest share of the total mass of a module. Therefore, it is precisely these two components that are usually recycled, along with the valuable silver from the conductors and contacts. The panel is shredded for this purpose and the broken pieces are then sorted. After the process, the high-quality silicon is too contaminated for it to be used in the manufacturing of new solar cells.
„80 percent of a panel – in terms of weight – must be recycled.“
IAN MARIUS PETERS
The fact that the materials cannot be separated cleanly enough during sorting, in turn, is due to the highly integrated design of the modules: “They are built to last, while they should actually be made for an eternal cycle instead,” says Peters.
In the C2C-PV project, which the European Research Council ERC is funding with €2 million, he is testing alternative processes for recycling solar systems. He started with a special type of cell consisting of components that can be separated again more easily: perovskite solar cells. With the help of metal-organic compounds, they convert sunlight into electricity particularly efficiently – relative to the thickness of the active layer. In addition, they offer another advantage: they are easy to manufacture. This is because, like a sandwich, they are made of individual layers that can be built up into a cell using common printing processes.
“The choice of solvent is crucial here,” says Peters. “If a new layer is applied, the solvent must not affect the layer underneath. In recycling, this process can be reversed, and layer after layer can be removed again one by one.”
While this method is not suitable for conventional silicon cells, however, the physicist is also looking for innovative ways to recycle these: “My ideal would be a circular process modelled on nature: in a forest, the leaves fall from the trees, they decompose on the ground and thus provide the material for new plants. If we can do that in photovoltaics, we could advance renewable energy to become a truly sustainable energy.”
„This would bring us quite close to the idea of a circular modular concept.“
STEFAN HAAS
To achieve this, the design of the solar modules themselves may have to change, Stefan Haas points out. Together with colleagues from the Central Institute for Engineering, Electronics and Analytics (ZEA-1), he is working at the Institute of Energy and Climate Research (IEK-5) on a concept to that end. His approach: solar modules that are designed for recycling from the planning stage onwards and that do not require plastics. Normally, each solar cell tile of a module is sealed with a transparent plastic film, which protects it from moisture. This coating interferes with recycling. In his design, Haas does without a lamination foil and instead encases the bare cells directly between the two glass panes of the module. To shield them from environmental influences, the edges of the glass panels must be hermetically sealed: “To achieve this, we apply a thin aluminium foil between the two glass plates on the very outside. We melt the metal briefly with a powerful laser. This is to ensure that the tiles are firmly joined together after cooling.”
REFINING THE DESIGN
Joining glass and aluminium already works in principle. In addition to optimizing the joining process, however, it is now also important to refine the design. This is because the plastic coating previously used also fulfilled a second function: it stabilized the module by damping vibrations and preventing the individual cells from shifting within the module. As an alternative, Stefan Haas wants to test disc-shaped spacers on glass that hold the cells firmly in place: “This would bring us quite close to the idea of a circular modular concept.”

Many wind power plants are also gradually becoming outdated and are being replaced by more powerful wind turbines. Whereas the steel of the mighty towers can easily be reintroduced into the raw material cycle, there is still a need for development regarding the rotor blades. They are difficult to recycle because they are made of a complex composite material: glass fibres or carbon fibres are embedded in a synthetic resin. Both components are subsequently difficult to separate from each other. New material systems that can be more easily recycled at the end of a wind turbine’s life cycle are currently being developed. Another example of materials with recycling potential are the concrete foundations of the towers, which extend up to four metres into the ground. The material can be ground up and given a second life in road construction – which, however, takes it out of the circular economy. This is not an optimal solution for the multiple recycling of the material.
A LOOK AHEAD
Jülich researchers are already thinking about recycling in another sector that is expected to play an important role in Germany’s energy supply: the production of hydrogen using electrolysis. It allows electricity from wind and sun to be converted into a storable form. The National Hydrogen Strategy envisages installing an electrolysis capacity of 5 gigawatts* in Germany by 2030. “So-called PEM electrolyzers are considered particularly well-suited for this purpose. They adapt flexibly to the current electricity supply,” explains Heidi Heinrichs of IEK-3. In the MATERIALIZE research project, which is funded by the European Research Council ERC, she is addressing the question of how material bottlenecks can be avoided in the global energy transition.
A wafer-thin plastic membrane separates the two electrodes of the PEM electrolyzer, where water is decomposed into oxygen and hydrogen. The membrane is coated with platinum on one side and iridium on the other – both critical, indispensable raw materials. “With ever more electrolyzers, and ever more powerful ones, the demand will eventually be so high, there won’t be a way forward without recycling, especially of iridium,” says the engineer. "But beyond that, we’ll probably also need devices that do not contain these critical materials. Alkaline electrolysis, which is already well established, puts itself forward for this. We should therefore focus on a mix of technologies, also with regard to the diversity of possible supply countries for the materials.”
10
gigawatts
is the electrolysis capacity targetto be met in Germany by 2030. This is what the National Hydrogen Strategy envisages.*
WASHING MACHINE FOR METALS
What such a process for recovering valuable materials from PEM electrolyzers could look like is being tested at IEK-14. There, Martin Müller and his team have constructed a “washing machine” with which the precious metals can be detached from the membrane surface.
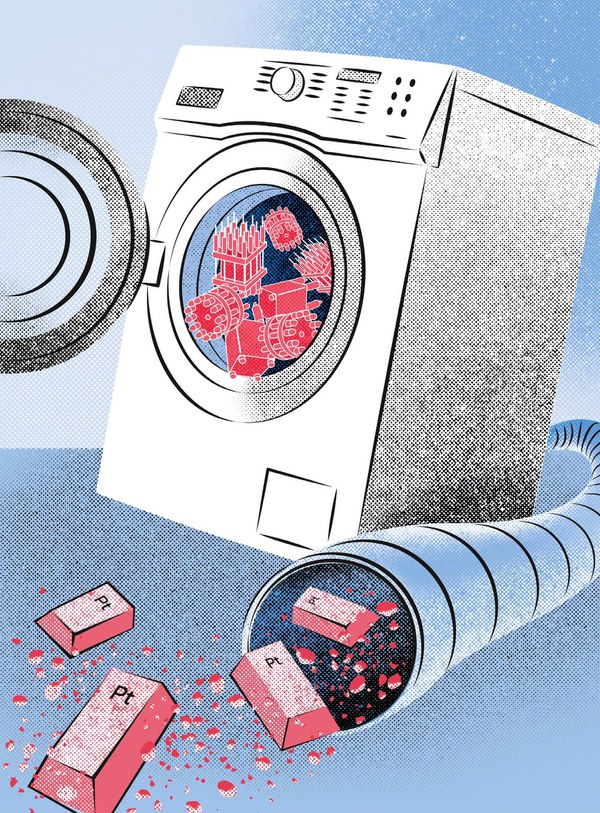
“With a mixture of water and alcohol, we can reclaim both the platinum and the iridium almost completely,” says the Jülich researcher. He was also able to prove in experiments that new membranes can be coated with the used catalysts. In principle, this brings the circular economy full circle.
High-temperature electrolysis (SOEC) can decompose water into its components even more efficiently than PEM electrolyzers. SOEC is particularly interesting when waste heat from other industrial processes is used to bring the cell to operating temperature and provide steam. In these cells, the two electrodes are separated by a ceramic solid electrolyte, which usually contains yttrium. It is one of the rare-earth metals.
“However, there are many different types of solid oxide electrolyzers,” says Stephan Sarner. “This makes recycling a challenge. Even if these cells don’t have a significant market share yet, a recycling-friendly design should be considered now.”
As part of ReNaRe, which is a joint project in the hydrogen lead project H2Giga funded by the Federal Ministry of Education and Research, the doctoral researcher from IEK-1 has developed a process to recycle the inner life of a certain type of cell. With the help of an acid bath, he first removes the layer that serves as the air electrode. “After that, around 85 per cent of the cell, with regards to weight, remains. We then recycle it as the starting material for new cells." To do this, the metallic and ceramic components from inside the cell are ground into a fine powder after an acid bath. This can then be added to the suspension from which new ceramic parts for the electrolyzers can be produced again. This means that the high-quality powders do not have to be resynthesized, thus saving resources, time, energy and costs.
So far, all of this is still done manually, but in principle, the process can also be automated. It could then serve as an important contribution to ensuring that renewable energies are not only fed from regenerative sources – but that the renewables themselves are renewed in line with the circular economy.
* as decided in the July 2023 update of the National Hydrogen Strategy
Text: Arnd Reuning | Illustrations: Bernd Struckmeyer